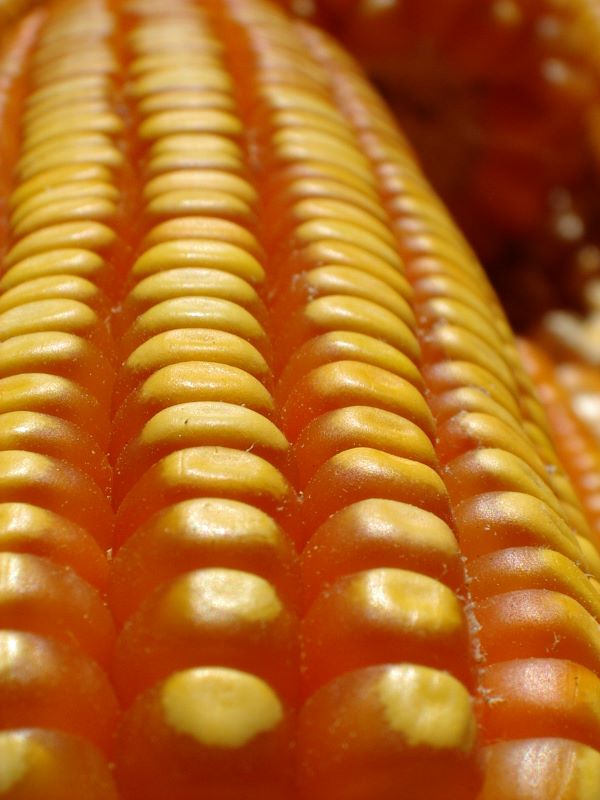
Foto: Eduardo Pinho / EMBRAPA
Enquanto o plástico derivado de petróleo leva, em média, 40 anos para se decompor, os biopolímeros demoram no máximo 180 dias
Os biopolímeros são uma das principais alternativas aos materiais plásticos derivados do petróleo. São produzidos a partir matérias-primas renováveis como cana-de-açúcar, milho, mandioca e batata, e óleos de girassol, soja e mamona. Com esse material, a indústria já produz sacolas, sacos para acondicionar alimentos e/ou lixo – cuja textura se assemelha às luvas cirúrgicas – e até produtos com mais rigidez, como pratos, copos e talheres.
Enquanto o plástico derivado de petróleo leva, em média, 40 anos para se decompor, os biopolímeros demoram no máximo 180 dias. Os materiais são biodegradáveis – se decompõem – mas os 100% orgânicos têm a vantagem de serem compostáveis, e se transformam em adubo. Isso porque, assim como outros materiais orgânicos, são ‘reconhecidos’ pelas bactérias que ajudam na decomposição.
Atualmente, a indústria brasileira de transformação de plástico tradicional produz 180 milhões de toneladas ao ano. São mais de 11.500 empresas, das quais apenas 6% com mais de 100 funcionários, que faturaram R$ 44 bilhões em 2010.
Projeções do Instituto de Pesquisas Tecnológicas (IPT) estimam que, até 2015, a produção de bioplásticos deverá atingir um milhão de toneladas, contra as 270 mil toneladas atuais. O principal entrave ao avanço mais rápido desse mercado ainda é o custo do produto, em torno de US$ 4,00 o quilo. Na opinião do empresário Marco Aurélio Amaral, sócio da Clean Living, “todo empresário quer salvar o planeta, mas são raros os que querem pagar por isso”. Segundo ele, o principal obstáculo ao crescimento desse mercado ainda é o preço, e para que o custo baixe, é preciso ter escala de produção e disponibilidade de matéria-prima. Por isso ele aposta no bioplástico produzido a partir de resina derivada de milho, uma lavoura tradicional no Brasil e com potencial de crescimento.
Principais biopolímeros produzidos no Brasil
POLÍMERO DE AMIDO (PA)
Produzido com matérias-primas como o milho, a mandioca, a batata ou o trigo. O amido desses grãos e tubérculos é retirado e passa por um processo químico de desestabilização e rearranjo da cadeia de moléculas, formando um material “plástico”.
POLILACTATOS (PLA)
Produzido a partir do ácido láctico feito por bactérias. Um caldo “açucarado” de fontes como melaço, açúcar de beterraba ou soro de leite, recebe bactérias que fermentam o líquido e produzem ácido láctico, transformado em plástico por meio de processos químicos.
POLIHIDROXIALCANOATO (PHA)
Produzido por bactérias que se alimentam de cana-de-açúcar, milho e óleo vegetal. Num biorreator, sob determinadas condições químicas, as bactérias alimentadas fabricam polímeros, que ficam armazenados em suas células. Muito utilizado na área médica.
Mandioca em forma de embalagem
Criada em meados de 2002, a CBPAK desenvolveu uma tecnologia para o uso do amido de mandioca como matéria-prima renovável na produção de embalagens e copos descartáveis, biodegradáveis e compostáveis. A empresa também instituiu um programa de conscientização de consumo junto a grandes empresas, visando reduzir o uso do plástico derivado de fontes não-renováveis. A ideia é que a CBPAK forneça 30 copos feitos com mandioca, por mês para cada funcionário e, após 30 dias, os recolha para dar o destino correto (compostagem). Segundo Claudio Rocha Bastos, fundador da empresa, a logística reversa foi a fórmula encontrada para tornar competitivo o custo dos copos à base de fécula de mandioca.
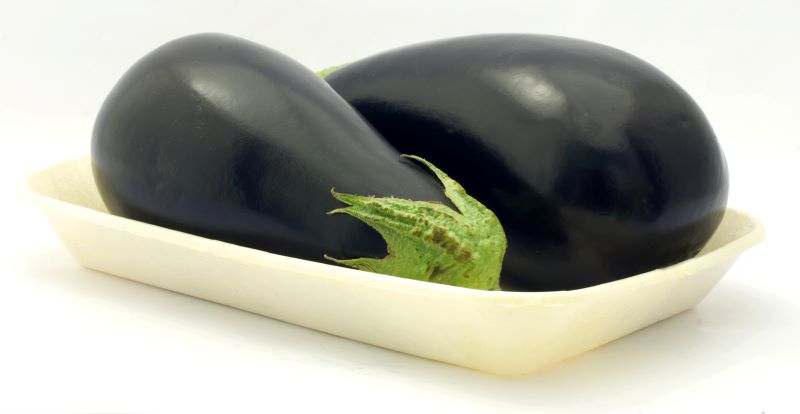
Bandeja feita de amido de mandioca – Foto: CBPAK
“Assim também contribuímos para reduzir a geração de passivo ambiental proveniente do descarte de embalagens e copos”, explica Bastos. Empresas de catering – terrestre e aéreo – como a LSG Skychefs, subsidária da Lufthansa e nova sócia da CBPAK –, grandes obras de engenharia, empresas brasileiras exportadoras de alimentos (a Europa já não aceita o isopor), grandes eventos e produtores de alimentos orgânicos e naturais são os potenciais consumidores das embalagens e copos biodegradáveis produzidos pela CBPAK, cuja certificação pela CETAL/ITAL-SP permite seu uso para acondicionar alimentos, inclusive quentes, resfriados e congelados.
A nova sede no Rio de Janeiro, inaugurada no início de 2012 em uma área de 1.500 m², tem capacidade instalada para fabricar até 2 milhões de peças por mês, 15 vezes maior que a anterior. A opção pela mandioca como matéria-prima levou em conta o fato de a cultura ser tradicional no Brasil (segundo maior produtor mundial), a grande capacidade instalada das fecularias (que transformam a mandioca em amido) e a estabilidade do preço do produto ao longo dos anos. Além disso, Claudio Rocha Bastos ressalta que a mandioca escapou da pauta internacional de discussões sobre a validade do uso de vegetais e grãos destinados à alimentação humana ou animal como matéria-prima renovável.
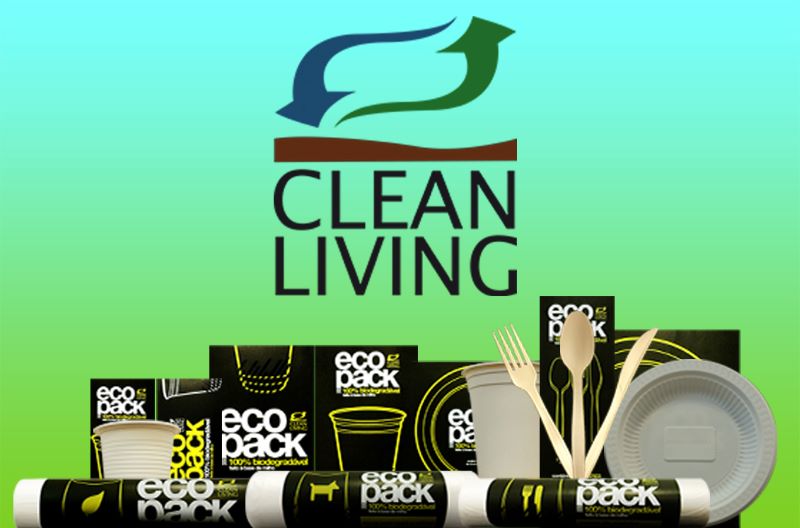
Linha de produtos confeccionados com o milho como matéria-prima – Foto: CLEAN LIVING
Opção pelo milho
A Clean Living investiu US$ 1,5 milhão em pesquisas de mercado no Brasil e no exterior, na compra de produtos para testes, no desenvolvimento da marca etc. Tudo para garantir o sucesso do projeto de lançamento, em 2009, de produtos à base de biopolímero de milho, importados da China. Ainda este ano, a Clean Living vai inaugurar uma fábrica e dar início à produção no Brasil, primeiro dos sacos de lixo e sacolas em geral e depois dos demais produtos da linha Ecopack, como talheres, copos e pratos. Também está nos planos da empresa credenciar outras indústrias, que atualmente trabalham com o plástico tradicional, para produzir os produtos de sua marca à base de milho.
A opção pelo milho foi devido à sua resistência e facilidade de moldagem. O plano de negócio se baseia em dar visibilidade à marca em lojas de varejo de consumo segmentado, como as especializadas em produtos naturais e saudáveis, e conquistar escala em grandes empresas e eventos, como a Rio+20, além de redes de fast-food e administradoras de planos de saúde, entre outros. “Precisamos começar a substituição pelos grandes geradores”, alega Marco Aurélio Amaral. Sua meta é conquistar pelo menos 1% do mercado até 2016.